以宝马i3为例,宝马用复合材料改变了电动汽车市场
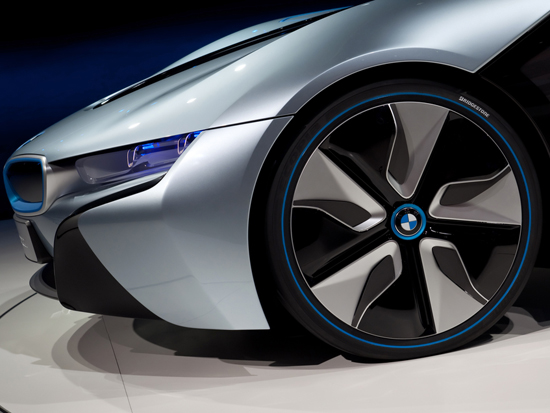
BMWi图像由Gyuszko-Photo通过Shutterstock.com。
燃油经济性受到汽车的重量大大影响。然而,多年来,我们的汽车越来越重。在美国,乘用车攀爬的平均遏制重量26%从1980年到2006年。由于重量增加等因素,动力系统技术的进步并没有导致每加仑汽油行驶里程的大幅提高。
但是,最近发布了宝马i3向轻量化的转变发出信号,这将有助于推动效率和电动汽车的竞争力.宝马在其新款电动汽车i3上使用了碳纤维增强塑料,与使用传统材料相比,车身重量减少了770磅,而且价格没有大幅上涨。其结果是一辆四人乘的汽车,一次充电可以行驶100英里,标价仅略高于4万美元。
并非巧合的是,宝马在开发其首款量产电动汽车的同时,还大举投资了一种基于碳纤维复合材料的新设计范式。
宝马的空白板岩
宝马知道,它不能仅仅在现有车型上安装电池和发动机。i3的电池组重量超过1000磅,因此减轻体重是抵消电池重量的关键。为了在现有的汽车上达到接近100英里(这是一个很有影响力的数字,通常被认为是电动汽车的可接受的最低距离)的续航里程,它需要一个非常大的电池组来移动那些沉重的钢铁。
这将进一步提高质量,进而要求更大的电池,等等,(且昂贵)的恶性循环,因为只是电池容量增加10%(相当于增加i3的范围约10英里)将增加约100磅的质量和1200美元的成本。此外,更大的电动汽车每行驶一英里就需要更多的能量,这使得其每加仑当量行驶里程更差,运营成本更高。
为了实现可能开始有效抵消所有电动动力传动系物的重量减少,宝马设计师知道他们需要重新思考车辆的设计。他们需要改变身体的形状,以更好地整合新的电动动力传动系统和电机,他们需要提供能够提供相同的结构完整性的材料。尽管碳纤维复合材料与钢相比,每磅较高,但每磅凭借新材料的结构优势节省的每磅省略电池组不必移动。为全新材料做出戏剧性投资的商业案例,拥有自己独特的结构特征,制造工艺,生产设施和供应链突然有意义。
宝马花了大约10年的时间,与新行业建立合作关系,垂直整合全球供应链,建立新的生产设施,并在现有车辆上使用碳纤维复合材料部件,以初步了解情况。目前,宝马每20小时就能生产一辆i3,这样每年就能生产400多辆车,按汽车行业标准算不算多,但这是一个重要的开端。而i3的售价只有4万美元左右,对于拥有价格临界点的主流消费者来说,它将是遥不可及的(PDF)30,000美元(虽然联邦和国家激励可能有助于将I3贴纸价格缩小到右侧市场的一些消费者的可接受数量)。
RMI扩展自动复合材料
和宝马一样,落基山研究所也认识到碳纤维复合材料的变革潜力。如果汽车行业大规模采用碳纤维,全球对碳纤维的总需求将迅速飙升,需要对颠覆性技术进行投资以降低这种材料的成本的材料公司将蜂拥而入,这些公司急于在自己最大的潜在增长市场获得立足点。
然后,诸如I3的整个车辆将变得更具成本效益,并且铺设了一个充满实惠的碳纤维密集型车辆的世界的方式比当今车辆更轻的,由电气化的动力提供动力,需要没有油并发出温室气体。我们可以扩展这一新材料行业的速度越快,愿景越快就会成为现实。
这就是RMI推出它的原因自动复合材料项目去年11月的研讨会上。该研讨会举办了45个关键决策者,来自汽车和碳纤维复合行业,所有这些都培训了识别现有车辆中碳纤维复合材料最有前途的近期应用。一台碳纤维复合部件仅在一辆车上加入了汽车需求,非常迅速创造踢投资所需的规模和增长,降低成本,刺激竞争和种子创新。
虽然许多部件提供了显著的用户价值,可以抵消较高的材料成本,但研讨会参与者确定的最有前景的应用是门内部,门的内部结构和框架,在碰撞时吸收冲击能量。在很大程度上,正是由于这种安全组件,车门内部的潜在价值达到了最高水平,因为碳纤维复合材料每磅吸收的碰撞能量是钢铁的六倍,客户愿意为安全支付额外的费用。由于碳纤维比钢更硬,结构构件可以做得更窄,同时提供相同的结构完整性。因此,窗框可以变得更薄,提供更多的能见度,并进一步增强碳纤维复合门内部的价值主张。最后,根据在车间进行的初始成本建模和价值量化,估计在门内部引入碳纤维所带来的巨大材料成本溢价将超过用户价值。
自11月的研讨会以来,RMI及其汽车工业同行,Munro&Associates,已经推出了AutoComposites商业化推出PAD(ACL),这是一个最有能力的碳纤维复合材料和汽车制造商的行业。内部内部是ACL的第一个商业化项目,八大公司已签署了设计,生产和测试。ACL旨在生产每年50,000个单位或更大 - 在任何行业中使用碳纤维综合达到的生产量 - 在2018年到主流车辆。ACL将能够推出并行商业化项目进一步加速学习并规模这个新的行业。
无论是在低体积或单个部件处的全碳纤维复合车辆在大容量下开头,目标是相同的:非常迅速缩放新材料行业,为改变的运输系统铺平道路,建立了广泛采用碳的无与伦比的轻量价潜力。好用的买球外围app网站纤维复合材料。
BMWi图像Gyuszko-Photo.通过shutterstock.com..
本文最初发表于岩石山研究所出口博客.