Why water is more expensive than most companies think
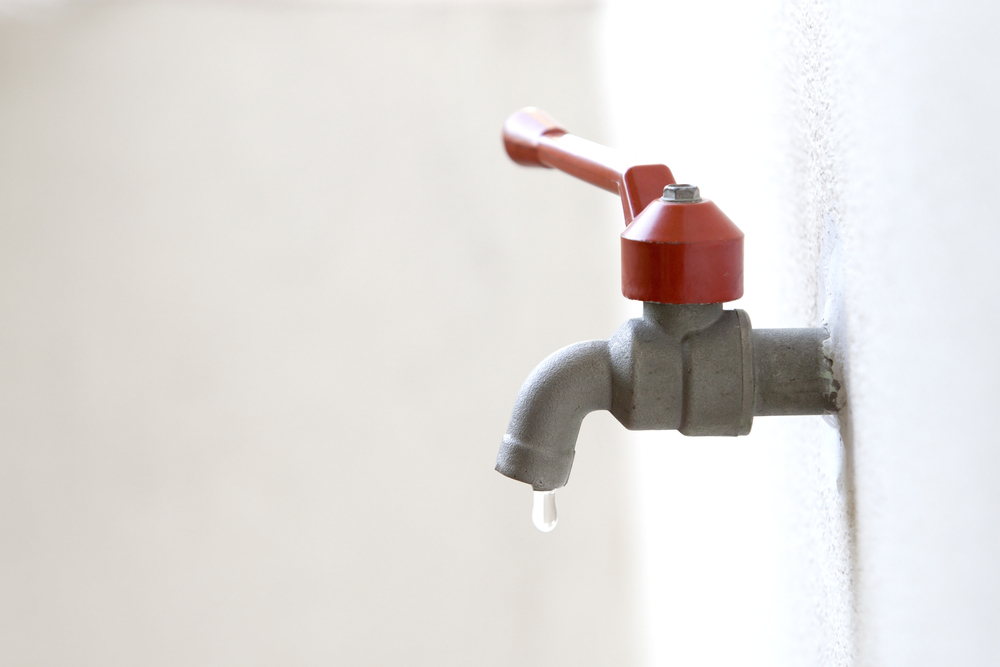
When it comes to managing their operations, savvy businesses know that efficient material use is crucial to improving the bottom line.
However, when it comes to water, many companies fail to plan for water shortages until the problem becomes acute.
Climate change and related changes in weather patterns, increasing urbanization and population growth are affecting water availability across the country. The U.S. EPA reported that water managers in 40 states expect water shortages in the next 10 years.
What is the true cost of water?
Contrary to prevailing wisdom, water isn’t cheap. What’s more, businesses pay twice for water — once when it enters the facility and again when it leaves.
In between, water is used for a variety of purposes, such as moving or rinsing products; changing or maintaining temperature; cleaning equipment, or preventing drying between stations of a manufacturing assembly line. The true cost of water usage can be $10-20 per 1,000 gallons after permit charges, discharge fees and treatment operational costs are taken into account.
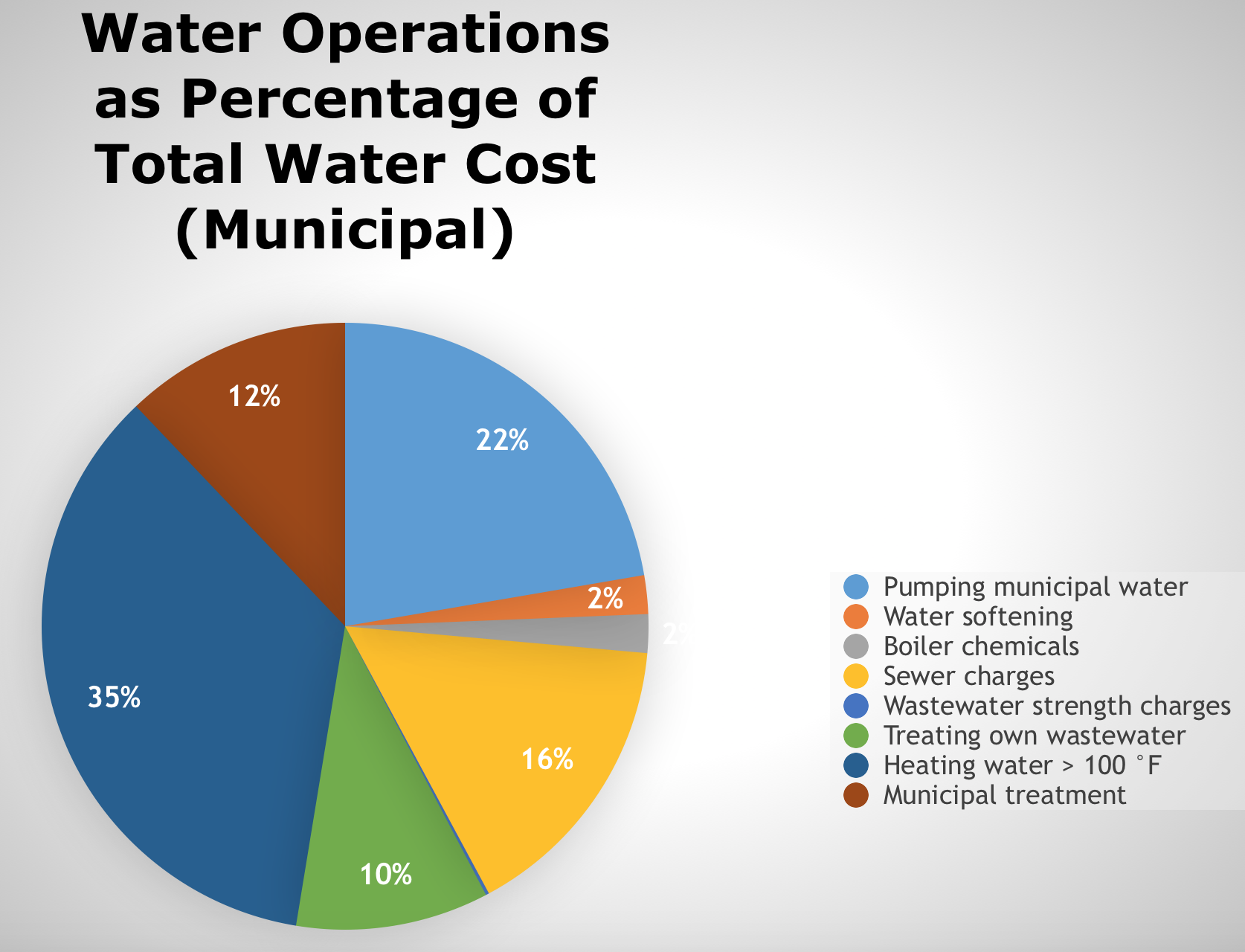
Over 30 years, the Minnesota Technical Assistance Program has helped businesses and communities conserve 600 million gallons of water.
的几个例子local measures: A printed circuit board manufacturer saved 5.6 million gallons and $33,000 a year by installing flow restrictors and new controls on the rinse tanks; and a facility that makes meat by-products switched to an air-cooled heat exchanger that recirculates in a closed loop, saving 4.5 million gallons and $13,200 annually.
Looking to unlock new savings? A few of our most trusted water conservation recommendations, beginning with the least expensive and ending with options that require capital investment:
- Use dry clean-up methods, such as dry sweeping, that reduce water use. These methods also may lead to possible reuse of waste materials and decreased sewage fees. Remember, water is not a broom.
- Check for leaks, especially if there’s a sudden spike or increase in water use without an increase in production. Routinely inspect and maintain equipment and lines to prevent surprise leaks.
- Optimize process design and parameters for new operating conditions if production or processes have been improved but water use has remained constant.
- Install automatic, timed or low-flow sensing devices, such as aerators and low-flow fixtures that stop or reduce water flow when not in use. Don’t forget your irrigation systems.
- Recirculate cooling water or switch to air cooling, if using once-through cooling.
- Recapture steam, which may allow recycling of waste heat and water for another process line if steam is a byproduct of the production line.
- Upgrade to efficient water treatment technologies when you need to replace equipment. These upgrades can cut maintenance time, chemical use and energy costs by reducing the amount of water subject to treatment.
- Reuse waste water from one process in another, if water is used in more than one line. Examples include using cooling tower effluent in exhaust scrubbers or irrigation ponds.
- Purify process effluent for water reuse. In addition to lowering water costs, this step could help recover valuable material from the waste stream and/or help meet discharge requirements.
To save money and ensure an adequate supply of water for your operations into the future, it’s just good business to start examining your water use practices today.